
5 Tips to Reduce Maintenance Costs
- Prevent breakdowns. Unsurprisingly, the best way to reduce maintenance costs is to prevent malfunctions. ...
- Track and manage inventory. If your average repair time is too high, one reason could be having a lack of spare parts in stock. ...
- Train your team. Another key to keeping maintenance costs down is training your entire team and not just the technicians.
- Choose the Right Technology. Even if your phone freezes from time to time and your computer may require a quick fix via the failsafe “On-Off” method, technology is an ...
- Extend the warranty/insurance period. Nothing functions flawlessly. It is always a good idea to insure the most expensive equipment for your business or to extend the warranty of some ...
- Follow Machinery & Equipment Guidelines. ...
- Focus on Preventive Maintenance. ...
- Use Maintenance Checklists. ...
- Keep Detailed Reports. ...
- Focus on Inventory. ...
- Expect the Unexpected. ...
- Invest in Training. ...
- Use Innovative Technology to Track Costs.
What is reducing maintenance costs?
Reducing Maintenance Costs is all about managing your maintenance strategy and planning more efficiently. Meaning that you would spend a little bit of extra time on scheduling work orders which will highly increase safety in the work environment. 2. Failure Data Analysis
What makes a maintenance project successful?
Any successful maintenance project must eliminate inefficiencies, increase work quality, reduce safety risks, and therefore reduce costs. VIZIYA has a great deal of experience, assisting many different companies across many different industries, to improve their maintenance processes.
Is it worth it to cancel maintenance?
There are certainly expenses associated with any maintenance project. However, cancelling them can be compared to dropping out of school to avoid paying another year’s tuition. You’re saving money today at the cost of reducing your future revenue. Selectively invest in maintenance!
What is the replacement value of my equipment?
Replacement value is not the same as what you paid for the equipment originally or its current depreciated value. For example, if your maintenance expenses for the past year total $5,000 for an excavator that would cost you $45,000 to replace, your maintenance cost/ estimated replacement value would be $5,000 divided by $45,000 — or 11 percent
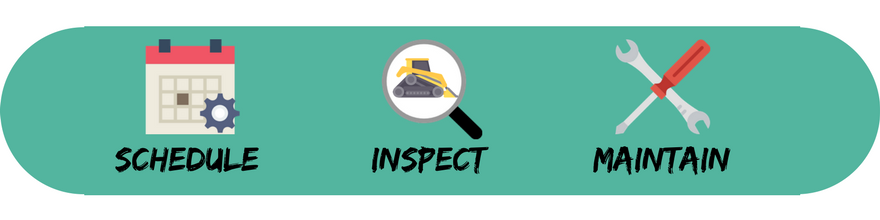
How can we reduce repair and maintenance?
Read our Top 5 Tips for reducing maintenance costs and start saving today.Prevent breakdowns. Unsurprisingly, the best way to reduce maintenance costs is to prevent malfunctions. ... Track and manage inventory. ... Train your team. ... Choose the Right Technology. ... Extend the warranty/insurance period.
How can O&M be reduced?
10 ways to reduce Operations and maintenance (OM) costsIdentify competitive markets. ... Optimize inverter design. ... Detailed system monitoring. ... Look for economies of scale. ... Clean panels regularly. ... Increase automation. ... Consider most the cost-effective service provider. ... Long-term offtake contracts.More items...•
How can we reduce the cost of equipment?
How to Reduce Equipment Maintenance CostsBe Aware Of Equipment Costs.Use Your Equipment Budget Wisely.Ensure the Proper Use of Tools.Prevent Tool Breakdowns.Train Your Service Personnel Well.Simplify Maintenance Procedures.Keep Track of Warranties.Track Your Equipment.More items...
What leads to high maintenance costs?
Neglecting regular maintenance—and not paying expenses for upkeep—may result in higher maintenance costs and, even worse, replacement costs for the asset itself. Individuals pay for maintenance on things like homes, automobiles, and appliances, while companies pay for upkeep on fixed assets and technology.
How can a business reduce operating expenses?
8 ways to reduce operating costs and expensesNormalize remote work. ... Save money on insurance. ... Consider a four-day workweek. ... Work smarter with technology. ... Outsource when necessary. ... Negotiate & shop around. ... Pay smart. ... Identify inefficiencies.
What is cost control in maintenance?
One of the most fundamental requirements of business operations is the ability to budget and control cost. This is especially so for the big-ticket functions in a plant's total cost. Maintenance, in many operations, is a cost well in excess of a million dollars every month.
How can we reduce the heavy maintenance cost of a computer?
How to Minimize Computer and Network Maintenance CostsUse Antivirus: Antivirus isn't foolproof, but it helps prevent many catastrophic problems from occurring. ... Keep a PC about 4 Years: After a computer turns four years old, it becomes more expensive to maintain it than it would be to simply purchase a new computer.More items...•
How can we reduce maintenance cost in SDLC?
One of the best ways to reduce maintenance costs is by implementing automatic monitoring tools that can monitor the performance of the system 24*7.
How do you calculate maintenance costs?
As you can see that the formula is very simple. You just need to take the amount spent on maintenance and repairs in, and then divide it by the total value of fixed assets in that same time frame. Maintenance and repairs refer to any money spent to keep your equipment and other fixed-assets in a working condition.
What type of expense is repairs and maintenance?
Repairs and maintenance expense is considered one of the operational expenses. It is recorded under the general and administrative expenses in the company's profits and losses statement during the period when it is incurred.
What are the components of maintenance cost?
Simply stated, maintenance costs include direct labor with benefits, materials, labor by contractors, and salaries and overhead. The sum of these components should be considered total maintenance cost. Each of these components has a definition that should be consistently applied.
What are the different types of maintenance cost?
One of the biggest maintenance costs for most organizations is labor. By labor, I'm not merely talking about wages and salaries....LaborWages and salaries.Benefits and bonuses.Training and development costs.Safety and incidents insurance and costs.Contractor costs.Emergency or overtime pay.
What is O&M strategy?
What is O&M Strategy Service? O&M Strategy Service is a turnkey outsourced solution to optimize your maintenance plans and execution for target assets. GE experts assess your goals, recommend an optimal plan and use APM software to help you drive sustained success.
What are O&M practices?
Introduction. Creating a best-practice operation-and-maintenance (O&M) program increases the efficiency of facility staff, improves building operational practices, and reduces utility costs.
What is O&M planning?
An O&M Plan specifies key system operating parameters and limits, maintenance procedures and schedules, and documentation methods necessary to demonstrate proper operation and maintenance of an approved emission control device or system.
What can O&M funds be used for?
Operation & Maintenance (O&M) Appropriations funds the cost of operating and maintaining equipment at a state of readiness. It covers expenses such as civilian salaries, travel, minor construction projects, operating military forces, training and education, depot maintenance, stock funds, and base operations support.
How to reduce maintenance costs?
Reducing maintenance costs often relies on cutting the budget. A better way to save money is to invest in selected maintenance projects.
How to save money on maintenance?
Six Methods to Improve Maintenance and Save Money at the Same Time 1 Improved reporting and analytics 2 PM planning and execution 3 Priority decisions based on asset criticality 4 Maintenance budgeting 5 Warranty claims 6 Planning and scheduling
How much more expensive is reactive maintenance than preventive maintenance?
Reactive work is recognized as being 3 to 5 times more expensive to conduct than properly planned preventive maintenance work.
What is maintenance budget?
Maintenance budgets are an attempt to balance the demands of the assets against the funds available. And curbing maintenance costs relies on far more than simply reducing the budget. The money available for maintenance is never unlimited, while the need for maintenance always increases.
Why is quality maintenance reporting important?
The sort of fine-grained data you can get from a quality maintenance reporting solution is invaluable. First, better information usually leads to better decisions. Second, having the data at your fingertips shows you where improvements can have the most impact. Third, it’s a great tool for convincing others. Management may not listen or care if you tell them that the maintenance team is overworked or needs an increased budget. However, they will find it harder to ignore cold, hard numbers.
What is profit minus expenses?
Profits are simply total revenue minus total expenses. This very simple equation means the choices come down to either increasing revenue or cutting expenses. Maintenance budgets are often a point of consideration for the later. Reducing maintenance costs often relies on cutting the budget. A better way to save money is to invest in selected ...
How much is the recovery on a new equipment warranty?
At $10 million dollars, your expected recovery on new equipment warranty claims is about $300,000. New parts, which cost you $5 million, have the lowest warranty recovery return rate at 1%. Even here, though, you can expect to recoup $50,000 in warranty claims.
How long does it take to cut maintenance costs?
The maintenance manager is often told that the maintenance cost must be cut by X%, within a time limit; 4-5% within 3-6 months seems to be the norm. Note that in most cases, if not all cases, no one knows what the ideal maintenance cost should be. We know it can’t be zero, but for some reason, we are convinced it can be lower and that it can be lowered right away.
What Should be the Main Goal for Maintenance Management if it’s Not Reducing Maintenance Cost?
Let’s look at the maintenance cost from one more angle. If reducing maintenance cost would be the key goal for a maintenance department, it is a very easy goal to achieve. Simply stop doing any maintenance, and your cost will be zero: goal achieved! Some may say that the idea above is silly; no mine, plant or mill would do that. Of course not, but why wouldn’t they?
Why is benchmarking maintenance cost futile?
Why? First, because the maintenance cost is extremely hard to compare between plants due to the variability of the following (as explained in the section above):
What would happen if one plant selected equipment with good maintainability, inspectability and reliability?
If one plant selected equipment with good maintainability, inspectability and reliability, it will have a lower maintenance cost than a plant that has not spent that investment upfront. If plants are completely different, it would be absurd to try to compare the maintenance costs.
What are some examples of maintenance consumables?
Common examples of this include air filters, oil filters for hydraulic units, refiner plates and chipper knives.
What happens if a plant is poorly maintained?
If a plant has been poorly maintained in the past and much maintenance has been deferred, there is a lot of maintenance to do in the future. Conversely, if the plant is well maintained, there is less maintenance to do in the future.
Why is it important to have a discussion about maintenance?
It is a critical discussion to have because it changes the whole approach to maintenance in an organization. The product of maintenance work should not be service, repair or cost; the outcome of maintenance work is equipment reliability.
How to improve safety of maintenance personnel?
Review training practices: Make sure that work processes are designed for maximum safety, and maintenance personnel is properly trained. Implement training for existing equipment, as well as new machinery or parts. Don’t cut corners when it comes to safety practices and operational training since equipment operators and technicians getting injured will cost you in more than one way. Safety first.
Why is it important to train non maintenance personnel?
If you’re using a CMMS system, set it up so non-maintenance staff can request repairs or report possible issues with equipment. Train them to identify common failures or potential problems.
What is the key factor in optimizing equipment?
A key factor is ensuring they are used for the purpose for which they’re designed.
Is maintenance management cost higher than net profit?
For some companies, especially in the manufacturing sector, maintenance management costs can be higher than the net profit in a year. Even if it seems impossible to cut costs, the right planning can make a difference. These expenses are controllable and some simple strategies can help reduce them tremendously, like using a computerized maintenance ...
Should you cut corners when it comes to safety practices and operational training?
Don’t cut corners when it comes to safety practices and operational training since equipment operators and technicians getting injured will cost you in more than one way. Safety first. Maintenance schedules: Not all breakdowns or repairs can be predicted, but preventive maintenance keeps them minimized.
What is predictive maintenance?
Predictive maintenance acts similar to failure prevention technology. As the word implies, it predicts problems before they happen. This involves the use of sophisticated technology that involves detailed analysis of various aspects of the machinery. Any possible flaw or inconsistency with regular patterns will be immediately detected.
What is failure prevention technology?
Failure prevention technology can detect possible flaws in equipment and cause the machine to shut down automatically. This will alert staff of a problem and so early action can be taken.
How to Reduce Your Hidden Maintenance, Repair, and Operations (MRO) Costs
In many cases, the company’s maintenance costs are so high that they can severely curb profit margins and prevent the company from blossoming. Your maintenance, repair, and operations (MRO) budget should not be one of the things that don’t let you sleep at night.
Addressing the Issue of High Maintenance Costs
The problem with organizations is the lack of proper reporting or documentation. Moreover, people who work on its development retire or leave without being replaced. Interestingly, the maintenance costs could be as high as three times compared to the cost of development.
What are the hidden costs that you need to take care of?
1. Unnecessary Consumption: Most MRO managers often consider the consumption of indirect items, tools, and supplies as a fixed cost. However, there are multiple areas and opportunities to reduce consumption, introduce controls, and reduce unnecessary inventories. When fewer MRO items are used, naturally, lesser money is spent.
Technologies that can Reduce These Hidden Costs and Save Your Day
Here are some technologies that you didn’t know needed to take care of your maintenance costs.
1. Reduces Expenses
Regularly schduled Equipment Maintenance and Repair Processes helps prevent critical breakdowns that may require high costs on your equipment.
2. Improve Operations
Tracking real-time location and live performance status of your machines allows you to make more efficient and accurate decisions for your business.
3. Manage Your Personnel
Equipment Management Systems should be appropriate and usable for your industry, company and employees. It should never make you lose time with difficult interfaces.
4. Minimize Your Risk
According to the reports of the U.S.A. National Insurance Crime Bureau, the construction sector loses more than $ 1 billion a year due to equipment and vehicle theft, and this number increases by 20% each year. Also U.S. National Equipment Records state that only 10% of stolen assets can be recovered.
What is maintenance cost?
This measure shows how much you are paying to keep your equipment running for a year in relation to what it would cost you today to replace it , either with the same equipment of similar age or, if not available, with a new machine. Maintenance costs include labor, material and overhead, but not fuel or depreciation.
How much does Ingalls reduce maintenance costs?
As a result, his clients reduce maintenance costs 25 percent to 50 percent or more. One construction client reduced maintenance costs by 52 percent with sound asset management practices.
What is an alternative to CMMS?
A spreadsheet computer program, like Access or Excel, is an alternative. Such a program can do many of the same functions as a CMMS. “However, if you can find a CMMS with a dedicated database designed by someone with a maintenance background, it will be more robust,” Ingalls says.
What do equipment manufacturers offer?
Equipment manufacturers offer training for maintenance supervisors and mechanics. They, in turn, can train the operators. An experienced, knowledgeable equipment operator can also help a new operator learn such maintenance tasks as inspection and lubrication. “Mem-ories aren’t very accurate, so make sure the operator follows a checklist when doing this servicing, so that nothing gets overlooked,” Ingalls advises.
What is the most important component of maintenance?
The single most important component of maintenance is inspection. “That involves knowing what you’re looking for and ensuring that your equipment is within the manufacturer’s specifications,” Ingalls says. “For example, is the bucket or belt in the proper condition?”
How much does it cost to test hydraulic oil?
Regular lab analysis of engine and hydraulic oil is a good way to head off expensive problems. Normally, it costs $25 to $30. “By measuring the types and amounts of metals from worn or damaged engine components and other contaminants in the oil, analysis can indicate any corrective action that’s needed,” Ingalls says.
How to assess how well you are maintaining equipment?
Another way to assess how well you are maintaining equipment is to compare the number of emergency hours (time dedicated to repairs that had to be completed within 24 hours) to total maintenance man-hours per year. The lower this figure, the better your maintenance practices. Comparison values: