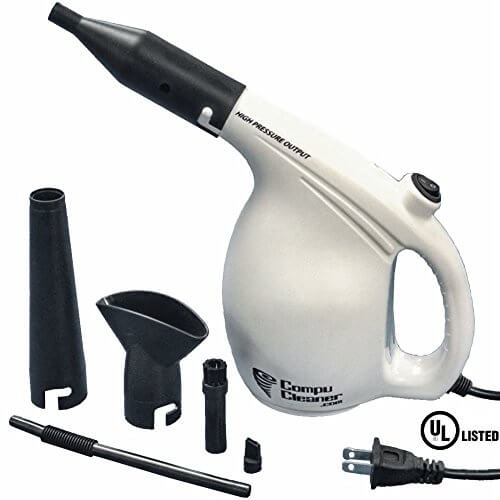
How to Repair a 12v Air Compressor?
- Step 1: Take it apart. Use a screwdriver to take it apart. Now, oil the bearings and wait until you remove the motor. You will find a very simple ...
- Step 2: Get the crankshaft out.
- Step 3: Start the main operation.
Full Answer
Is it hard to fix a 12V air compressor?
In such case, it may be hard to discover how to fix 12v air compressor. If you can’t achieve the necessary pressure when trying to inflate tires, it’s possible that the cause of the problem may be in valves too. The various contaminants can accumulate below them that interfere with good conformity.
How to repair an Air Compressor tank?
Welding an air compressor tank is the most effective way to repair any leakage. Just make sure you have the right welding setup for the tank thickness. Lastly, repair the tank after you have turned it off and release all the pressure.
How does a 12V air compressor work?
While the piston is traveling upwards, the pressure closes the one-way reed valve, and pressure builds up until it is pushed through the one-way valve that is connected to the gauge, and output barb, travelling to the chuck. 9 times out of 10, with inexpensive 12V compressors, the entire assembly simply lifts out.
How do you fix an air compressor that won t start?
Tighten the switch with a wrench and hold the stub pipe from the tank with a pliers. If your air compressor starts up fine on the first start of the day, but stalls and makes a loud humming sound on subsequent tries, you’ve got a bum “unloader” valve.
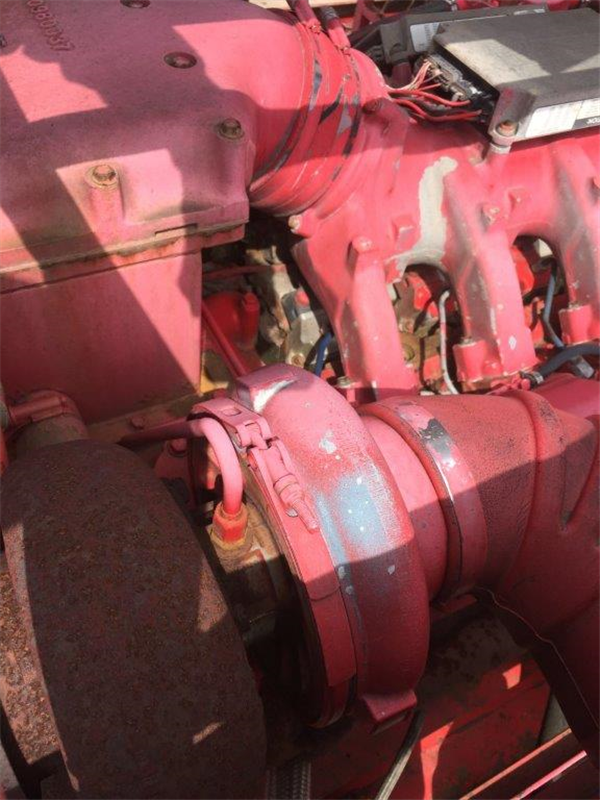
Can an air compressor be repaired?
Air compressor repair can be simple. The air compressor unloader valve is what makes the “psssssst” sound when the motor shuts off after reaching operating pressure. It's actually venting the residual pressure from the compressor head so the motor doesn't have to work as hard on the next startup.
What causes an air compressor to stop working?
An air compressor problem could stem from one of many issues, such as an air leak, an oil leak or a broken part. In some cases, you might have insufficient pressurization or air flow. In other cases, the compressor might fail to start up or stop running as prompted.
How do I troubleshoot my air compressor?
Insufficient pressure at point of use.Leaks or restriction. Check for leaks or restriction in hose or piping. Repair.Restricted air intake. Clean or replace air filter element.Slipping belts. Tighten belts.Service hose too small. Replace with larger hose.Excessive air requirement.
How do you fix an air compressor that won't start?
0:114:50Air compressor wont turn on? Try this! - YouTubeYouTubeStart of suggested clipEnd of suggested clipItself is good uh typically if you've got all that and as long as this motor itself is good thenMoreItself is good uh typically if you've got all that and as long as this motor itself is good then when you turn it on it should kick on and fill up and this compressor.
What is the most common cause of compressor failure?
Overheating is a common cause of compressor failure, and there are many factors at play. If direct sunlight falls on your outdoor unit and there is inadequate ventilation around it, it makes your unit's compressor overheated. High voltages can also damage the motor causing the compressor to overheat.
How do you reset an air compressor?
0:000:55How to reset/restart your air compressor when it won't startYouTubeStart of suggested clipEnd of suggested clipAnd maybe other brands as well is a it has a hidden thermal reset button that if the the motorMoreAnd maybe other brands as well is a it has a hidden thermal reset button that if the the motor overheats is going to pop out and will stop you turning it on because.
Does an air compressor have a fuse?
Some air compressors have reset switches while others will have in-line fuses that need to be checked. To find them follow the line of power from the air compressor back to the outlet. If you find a blown fuse or tripped breaker go ahead and either replace the fuse or reset the breaker.
How do you test a pressure switch on a air compressor?
Checking Your Air Compressor Pressure SwitchStart the testing process by unplugging your air compressor.Next, unscrew and remove the housing from your unit.Disconnect the sets of wires running between your pressure switch and the terminal block. ... Be sure to leave the black-and-white wires connected.More items...•
How do you rebuild an air compressor motor?
1:022:35How to Rebuild an Air Compressor Pump - YouTubeYouTubeStart of suggested clipEnd of suggested clipThe piston out of the cylinder sleeve remove the Torx screw from the top of the piston remove. TheMoreThe piston out of the cylinder sleeve remove the Torx screw from the top of the piston remove. The piston cap and compression ring place the new compression ring on the top of the piston reinstall.
How do you know if an air compressor fuse is blown?
Blown Fuse or Tripped Breaker When an air compressor is causing an electrical fault a fuse will blow or it will trip the breaker system. If that's happened there is no electricity going to your air compressor. Some air compressors have reset switches while others will have in-line fuses that need to be checked.
Do compressors have reset buttons?
A reset button can be found inside the air conditioner's compressor. Typically, the button is red in colour and modest in size.
How do you know if your air compressor valve is bad?
If a check valve fails in its open position, it can allow air to leak back from the header into the compressor when it's not running. This, in turn, can cause the compressor to spin backwards, thereby damaging it in the process. More often than not, however, we see check valves fail when they're closed.
How do you test an air compressor motor?
0:3813:08Air compressor motor troubleshooting Part 1- bad start capacitor switchYouTubeStart of suggested clipEnd of suggested clipAnd make sure there's no mechanical binding or or anything like that that's keeping the machine fromMoreAnd make sure there's no mechanical binding or or anything like that that's keeping the machine from turning and it's not the unloader valve working.
How to take apart a compressor?
Step 1: Take it apart. Use a screwdriver to take it apart. Now, oil the bearings and wait until you remove the motor. You will find a very simple mechanical assembly inside the compressor. You will see-. 1. A motor turns a gear which is connected to a crankshaft. 2.
How long does it take to charge a 125 PSI compressor?
It will begin to charge the tank to 125 PSI, which will take about 4 minutes. 5. When the tank is fully charged to 125 PSI, switch on the ball valve. 6. While pumping begins, the air pressure in the tank will drop to 90 PSI. Then the compressor will recharge to 125 PSI or to the selected pumping rate.
How to connect air compressor to car battery?
If you don’t know how to connect the air compressor to your car battery, you’ll know now! 1. First of all, connect the pressure line from a pump control unit to the pressure outlet on the 12v compressor. 2. Make sure, the on/off switch is in the off position before you connect it to the power source.
How to remove factory hose from a barb?
For removing the factory hose, insert a small screwdriver into the collar and between the collar and the hose. Continue doing this until the collar splits in half.
Can you use a Q tip on a crankcase?
Once you are done with getting the crankshaft out, you’ll freely lubricate the crankcase. In case you don’t have a flavor injector, you can use a Q-tip, but it will not do as good of a job.
How to get piston out of crankcase?
The piston travels all the way to the top of the cylinder. Slip the connecting rod through the top of the cylinder, and push the piston in. Keep the piston inside the cylinder, and then angle the connecting rod slightly to get it into the crankcase and onto the lower end rod bearing sticking out of the crankshaft.
How to remove a factory hose?
To remove the factory hose, simply insert a small flathead screwdriver into the collar between the collar and the hose. Do this several places until the collar splits in half. Simply remove the collar and pull the broken hose off of the barb. This frees you to put the good hose back on.
How does grease affect tire pressure?
The piston goes up and down very quickly and a lot of heat is generated. A good amount of grease here will increase the pressure output , the life of the piston, and inflate tires much quicker. Look at the wear pattern in the cylinder. If you can see an area that isn't worn, that area goes toward the crankcase.
How many screws does a commutator pump have?
This is because you forced the commutator to grind the dust away from the brushes and created a new electrical connection. Anyway... This particular pump has 3 cy linder head screws. Most inexpensive pumps only have 2, and some don't even have the cooling fins on the cylinder head.
What is the gear that turns a motor?
A motor turns a gear that is connected to a crankshaft . The crankshaft is supported by two bushings, and has a shaft that is connected to the connecting rod. The connecting rod is connected to the piston, which moves up and down in a polished metal cylinder.
Can you put a piston back on a crankshaft?
A word to the wise: Don't bother putting the piston and connecting rod assembly back onto the crankshaft until you have inserted the piston into the cylinder first. The rubber crown on the piston will only allow it to go in one way! Grease up the cylinder, and the crown of the piston.
Air compressor stalling? Save money and fix it yourself
A faulty air compressor unloader valve can cause the compressor to stall out, but replacement valves are readily available and the fix is easy and inexpensive.
Replacing the unloader valve
Slap two open end wrenches on the compression fitting and loosen the nut on the air line. Pull it out of the fitting.
Required Tools for this Compressor Repair Project
Have the necessary tools for this DIY project lined up before you start—you’ll save time and frustration.
Required Materials for this Compressor Repair Project
Avoid last-minute shopping trips by having all your materials ready ahead of time. Here’s a list.
Detect Your Air Compressor Tank Leak
One of the most common ways to check if your air compressor tank is leaking air is to hear it closely. Try implementing a system in which someone will walk close to the tank and search for any hissing noise, probably on a weekly basis.
How to Fix an Air Compressor Tank Leak?
Get all the necessary tools at your hand or close so you can access them quickly in time of need. For fixing air compressor leakage, we will need-
How to Reduce an Air Compressor Tank Leak
Ensure all the air compressor fittings, hoses and tubing are all properly rated and high quality.
Frequently Asked Questions
Repairing an air compressor tank is a fairly easy task as long as you have the right tools. Nevertheless, if the leaking area is large or internal components sustain severe damage, it can be hard to repair. You will need professional tools and expertise to repair it properly.
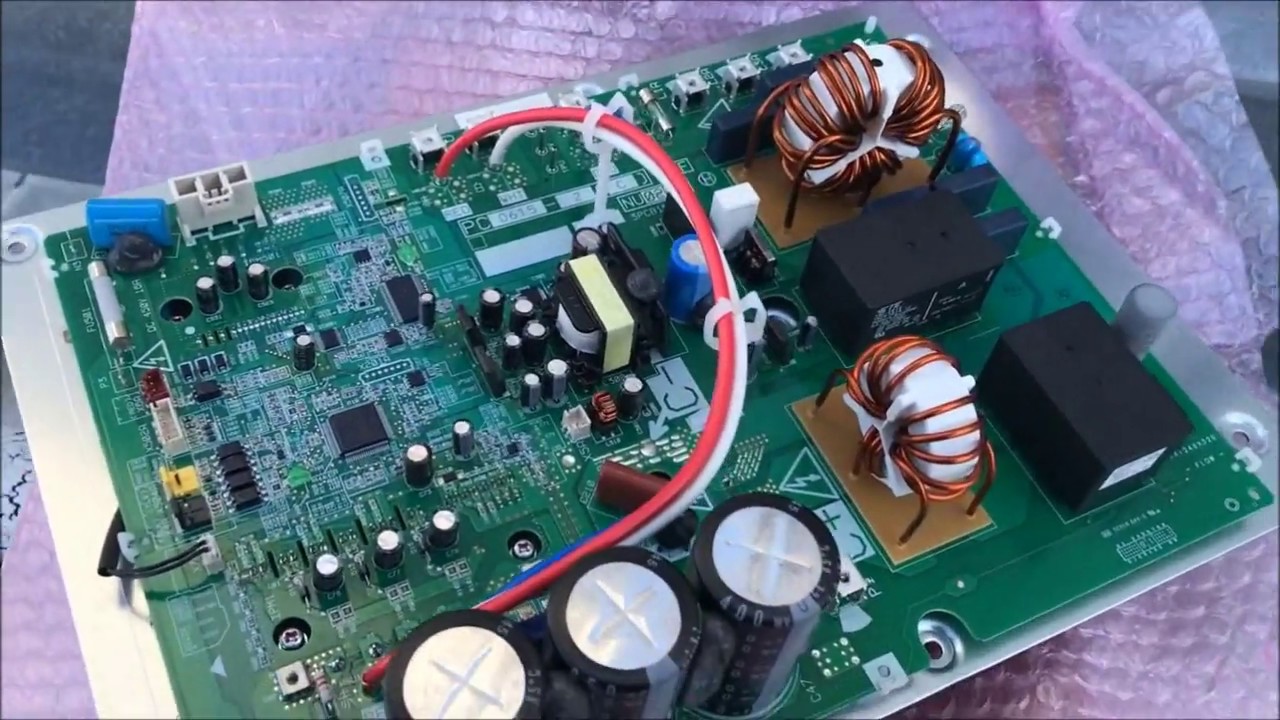