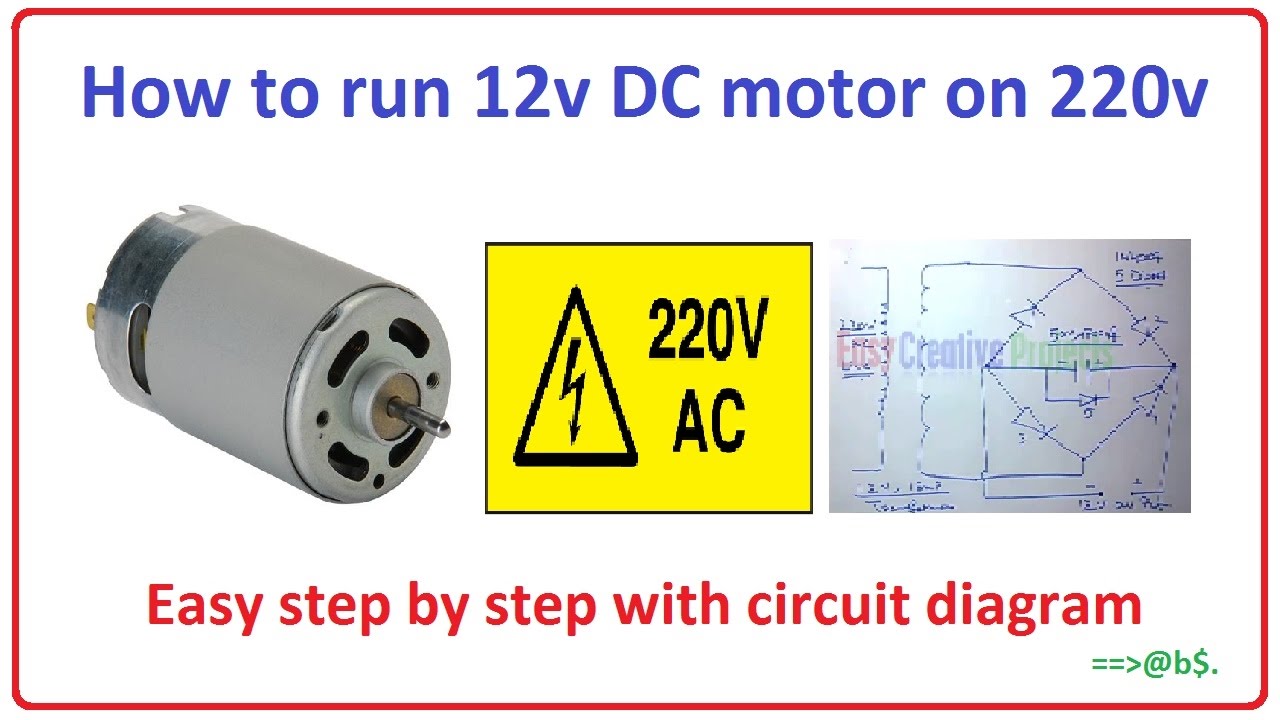
How do you make a 12 volt motor work on DC?
You can make an easy experiment using a small DC motor: connect it on a DC power supply of nominal voltage of the motor (ex. the power supply is 12V and power up a 12V motor). Now squeeze the shaft and the speed is going down, let it free and the speed is going up again to the specific value of speed for 12V. How many watts is a 12 volt motor?
Do I need to rewind my electric motor?
If not, a rewind will be necessary, a job that is beyond the capabilities of most general maintenance shops. The standard way to test winding insulation is the megger test 16 which applies a D.C. voltage, usually 500 or 1000 volts, to the motor and measures the resistance of the insulation.
What causes a DC motor to fail?
Worn out brushes are a common reason for DC motor failure. Our team would also carefully inspect for other defects that may contribute to the damaged motor. Once we have made the necessary rebuild, rewind or repair on the DC motor, we will test it to ensure it is functioning optimally to its rated load.
Can your repair technicians repair DC motors?
Our repair technicians are trained to abide by strict procedures at all times when troubleshooting and repairing DC motors. We make sure that the power is disconnected from the DC motor before we start our preliminary inspections. A non-powered DC motor can still be dangerous, as the internal capacitors may still hold a charge.

Can a DC motor be repaired?
DC motors often have to have field coils and armatures rewound and insulated. In some cases, repairs can be made but, sometimes, rewinding is necessary to achieve acceptable motor performance.
How do you test a 12 volt DC motor?
2:456:32Testing 12 volt DC motors anywhere. How to test marine or car ... - YouTubeYouTubeStart of suggested clipEnd of suggested clipYou want to make sure your pin is touching against the terminal. They're setting their good spreadMoreYou want to make sure your pin is touching against the terminal. They're setting their good spread apart. And then my orange wire i'm going to do that with. Positive.
How do you test if a 12v motor is working?
0:502:49Testing A 12v DC Motor For An Open With A Test Light - YouTubeYouTubeStart of suggested clipEnd of suggested clipI took a power wire kept. It simple red to power black as ground ran power to the motor. Comes. BackMoreI took a power wire kept. It simple red to power black as ground ran power to the motor. Comes. Back out ground hooks to my tests light and the test site hooks my jump pack.
How do you troubleshoot a DC motor?
0:301:41Troubleshooting a Brushed DC Motor - YouTubeYouTubeStart of suggested clipEnd of suggested clipAnother test that could be performed is to run the motor using a 9-volt battery connect the positiveMoreAnother test that could be performed is to run the motor using a 9-volt battery connect the positive terminal of the 9-volt battery to the positive terminal of the motor connect.
How do you tell if a motor is burned out?
When a motor burns out, a short circuit occurs in the windings and the motor ceases to turn. You can test for a short circuit by checking the resistance of the windings with an ohmmeter; a reading of 0 ohms (Ω) indicates a short.
How do you know if your electric motor is bad?
How To Check If an Electric Motor Is Going BadCheck the Bearings and Shaft. A motor's bearings are one of the most common components to go bad. ... Inspect the Motor Windings With a Multimeter. ... Test the Power With a Multimeter. ... Ensure the Fan Is in Good Shape and Secure.
How do you test a DC motor with a multimeter?
1:134:27Learn how to test DC Motor with multimeter - YouTubeYouTubeStart of suggested clipEnd of suggested clipSo let's test these two motors using the multimeter of course. So first of all you should locate theMoreSo let's test these two motors using the multimeter of course. So first of all you should locate the positive terminal on the negative terminal.
Why motor winding is failure?
The most common cause of motor failure, and arguably the most difficult to overcome, is low resistance. Low resistance is caused by the degradation of the insulation of the windings due to conditions such as overheating, corrosion, or physical damage.
How does a 12 volt motor work?
1:514:49DC Motor, How it works? - YouTubeYouTubeStart of suggested clipEnd of suggested clipContact with the power source a permanent magnet stator pole is used only for very small dc motorsMoreContact with the power source a permanent magnet stator pole is used only for very small dc motors most often an electromagnet is used the field coil of the electromagnet is powered from the same dc.
What is the most common cause of motor failure?
Winding insulation breakdown and bearing wear are the two most common causes of motor failure, but those conditions arise for many different reasons....Shaft imbalanceDirt accumulation.Missing balance weights.Manufacturing variations.Uneven mass in motor windings and other wear-related factors.
Why do DC motors fail?
High levels of humidity can cause corrosion within the bearing which causes increasing level of friction which has a growing effect on wear. This may damage the shaft and the bearings restricting the smooth rotating operation of the motor which can affect speed and torque.
What are the things that needs to be tested when troubleshooting a DC motor?
For the motor, test the stator winding resistance phase-to-phase and phase-to-ground....Final tests and procedures.Listen for unusual noises.Smell for smoke or hot insulation.Feel the motor for excessive heat or vibration.Look for possible obstructions.
How do you test a DC motor with a multimeter?
1:134:27Learn how to test DC Motor with multimeter - YouTubeYouTubeStart of suggested clipEnd of suggested clipSo let's test these two motors using the multimeter of course. So first of all you should locate theMoreSo let's test these two motors using the multimeter of course. So first of all you should locate the positive terminal on the negative terminal.
How do you check voltage on a DC motor with a multimeter?
How to measure dc voltage with a digital multimeterThen insert the red probes into the V Ω jack. When finished, remove the probes in reverse order: red first, then black.Connect the test probes to the circuit: black to the negative polarity test point (circuit ground), red to positive test point.
How do you test a motor with a multimeter?
Set your multimeter to Ohms. Start by completely disconnecting the spindle motor from all power sources. Check each wire, including T1, T2, T3 and the ground wire. If the reading is infinite, your motor should be fine.
How do you measure the resistance of a DC motor?
You can measure your motor's DC resistance with a multimeter, but not directly, because the value will be very low (~0.05 Ohms). To get sufficient resolution you need to feed about 1 Amp into a motor winding, while measuring the voltage across it. If the current is exactly 1A then the resistance equals the voltage.
Step 1: Clean It
If it needs it clean it with scotchbrite and soap to remove any corrosion and goo it doesn't matter that it gets wet you're going to strip it completely and dry it thoroughly anyway.
Step 2: Take It Apart
Place a small blunt blade between the drive gear and casing and leaver the gear off. Using a very small flat bladed screwdriver unbend the tabs securing the back to the case and pull it off. Push the drive shaft down on the table grip the armature and with draw it from the body of the motor it will kick sideways as it comes free.
Step 3: Clean and Examine
I used disposable paper tissues for most of my cleaning kitchen towel or cotton rag would work as well. Notice the green goo the colouration is due to copper salts and possibly beryllium salts both of which are toxic ( I am possibly over stating this but it is better that you know than don't) Check the brushes are intact if not there replacing them is not impossible but is not covered by this instrucable set aside for further work. wipe clean the commutator armature and shaft assembly use a solvent if required, I tend to use lighter fuel the liquid type not gas as my cleaning solvent of choice isoprop will probably do as well but avoid acetone/cellulose thiners or white spirit as these could damage cheap laquer on the windings.
Step 4: Repairs
All motors will be different but on this one the brush carrier is a separate unit from the back plate located on a pin and in a slot in the back plate to remove it was simply a case of putting my thumb nail in the joint and pushing you may wish to use a small screwdriver or knife blade. clean the back plate and brush carrier again I used lighter fluid and tisue paper. Source your replacement cable I used a strand from an old ribbon cable, strip a short length of insulation and bend the stripped end at a right angle.
Step 5: Reassembling
apply a drop of light oil to the front bearing shaft grip the armature and commutator assembly by the commutator and reinsert into the case keep a firm grip on both as the field magnets will make it kick around.
Step 6: Other Motors 1
having recently rationalised my pile of salvage cd drives into useful parts I thought I'd open one of the small motors up to show the intervals of small brushed motors are similar. This one (there are actually photos of 2 different motors here one with attached wires one that was soldered to a pcb) operated the tray mechanism.
Step 7: Larger Motor
this step will be added next time I have cause to disassemble something bigger.
What can go wrong with a DC motor?
Let’s face it, there is a lot that can go wrong with a DC motor, but most of it involves fairly straightforward repairs, such as bearing replacement or a simple brush replacement. These repairs won’t take as long as a more complicated repair like an armature or field coil rewind. Keep in mind, however, that a fast repair isn’t always a good repair. Quality DC motor repair shops will work to track down not just what is wrong with your motor but what caused it to fail in the first place. This takes time, as does redesign for improved performance and careful quality testing. The extra time invented in repair will, in turn, result in significantly better downtime and much better motor performance.
What are the different types of DC motors?
The four types of DC motors are shunt wound motors, series wound motors, permanent magnet, and compound motors. Shunt motors are typically used for speed regulation made possible because the shunt field can be excited separately from the armature windings. Series motors generate excellent starting torque but don’t offer much in the way ...
Why is my commutator burning?
Marking and burning on the commutator can indicate issues with the DC motor. Slot bar marking can be seen as every other or every few commutator bars being darkened and discolored. This is from an uneven current distribution or a bad armature winding. Burning of the commutator bar edges indicated that there is incorrect brush alignment, bad interpoles (if applicable), incorrect brush grade, or even low spring pressure. You may also see copper drag happen which looks like you smeared the copper of the commutator with the brushes. This is due to excessive heat that softened the commutator surface. This is an indicator of a potential larger issue.
How do armature coils work?
The ends of the armature windings are connected to a commutator which allows each of the armature coils to be energized in turn via carbon brushes (except in the case of a brushless motor, which makes use of electronics to achieve the same effect).
Why does my commutator brush groove?
This is usually caused either by arcing due to an incorrectly installed brush (low spring pressure) or the use of the wrong type of brush (abrasive).This can also be caused by low humidity and temperature.
Why do motor brushes wear out?
Worn brushes can cause loss of power to the armature, damage to the armature winding, and damage to the commutator. Premature motor brush wear can result from incorrect installation as well as issues with the windings, voltage surges, overloading, and sparking. An added complication from carbon brush wear is the generation of carbon dust which can lead to grounding of the field coil or armature winding.
What causes motor brush wear?
Premature motor brush wear can result from incorrect installation as well as issues with the windings, voltage surges, overloading, and sparking. An added complication from carbon brush wear is the generation of carbon dust which can lead to grounding of the field coil or armature winding.
What causes a DC motor to fail?
As simple as it is, the DC motor involves moving parts that may eventually fail. A DC motor that was previously running but broke down may have its brushes worn down is and no longer making contact with the commutator. This causes a lack of current being passed through the coil and as a result, no torque being generated.
When is a DC motor deployed?
Again, this is done in a safe environment as the moving parts of a DC motor may cause injury. The DC motor is only deployed when it passes our test satisfactorily.
Why does my conveyor belt fail?
Most production facilities rely on an operational conveyor system to ensure orders are met within the specified schedule. Powered by DC motor, these conveyor belts may occasionally fail, and the culprit could be the motor itself. You may be pressured to get the conveyor belt in order again, but it helps to understand why the DC motor fails.
Can a DC motor be damaged?
In some cases, a DC motor can be damaged by improper installation. When the armature is not properly aligned it may brush against the magnets and cause serious damage to the motor itself. The environment that the DC motor operates in can also cause the motor to fail.
How to remove springs and brushes?
Remove the springs and brushes by removing the cover typically with a slotted dcrew driver
Do you put the brush back in the same hole as the motor?
Note before removing DC motor brushes- always put the brush back in the same hole of the motor. They provide the most surface contact since they are worn in.
How to clean windings for motor?
Once again, look at the physical condition of the windings. If they are dirty or corroded, clean the windings with a brush, hot water and detergents and a vacuum. 14 Check the manufacturer’s documentation before using any solvents or detergents to ensure they will not damage the insulation. Avoid using pressurized air because the force of the air may propel particles into the winding insulation and damage it. Is there moisture on the windings? If so, prior to conducting any winding tests, the windings must be thoroughly dried out. Moist or wet windings will generally give false readings when conducting insulation tests so the windings must be dried first. This is done by baking the motor windings in an oven until the insulation resistance is at least 10 megohms. Refer to the manufacturer’s technical documentation on specific requirements. If this does not work, consider revarnishing the motor first. 15 If the motor passes the insulation tests, this is an adequate solution. If not, a rewind will be necessary, a job that is beyond the capabilities of most general maintenance shops.
Why does my motor make a noise?
Noises and vibrations are not limited to mechanical problems or imbalances; electrical imbalances , such as open or shorted windings or uneven airgaps, can cause noises or vibrations. The easy way to troubleshoot an electrical from an mechanical imbalance is to first power up the motor, then disconnect power.
What type of bearings are used in low horsepower motors?
There are lubed-for-life, sealed bearings used in low horsepower motors that do not require lubrication. 28
How to clean bearings before replacing?
Prior to bearing removal or replacement, clean the housing with solvents or flushing oils. The bearings should be cleaned with a lint free rag . Take a lot of care to keep dirt out of the bearing. When bearings need to be replaced, remove them with the proper tool.
Is a ground insulation test a motor?
A ground insulation test is not a comprehensive motor insulation test; it does not, for instance, test the insulation’s resistance between turns of the windings. To test coil-to-coil or turn-to-turn insulation failures, a high surge test, the Hipot test, would be required and requires special test equipment 19.
