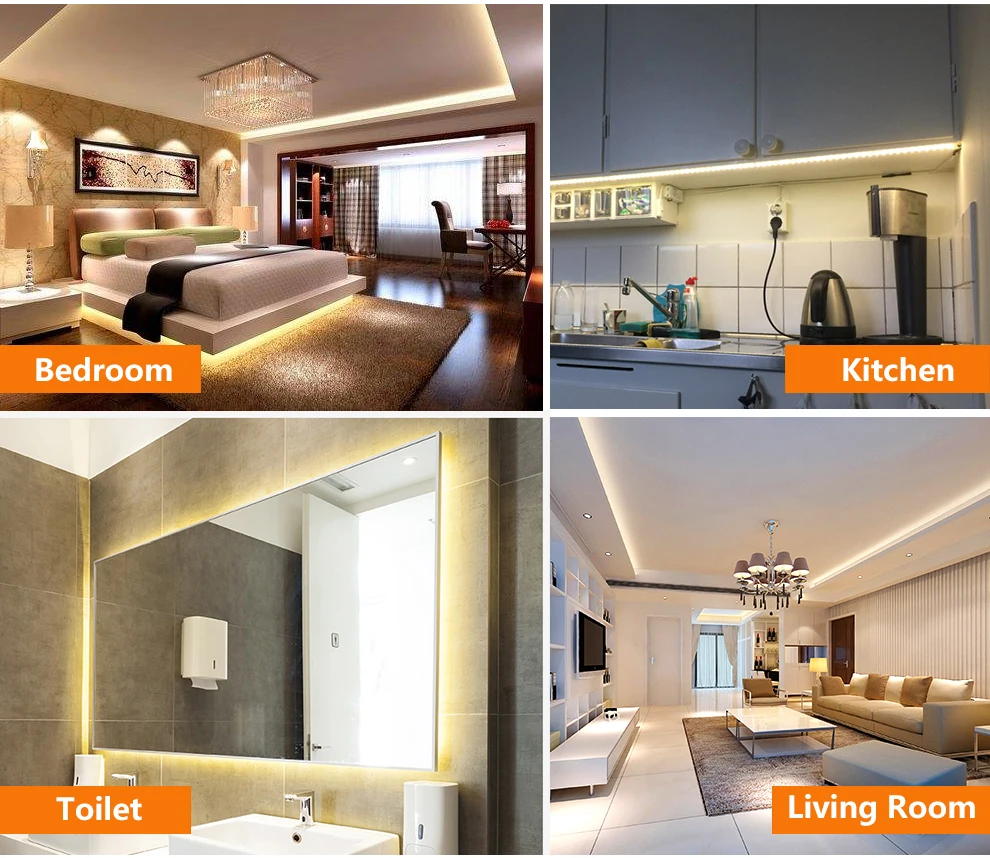
Clean all the shavings out, and slip a coupler on. Braze both sides of the coupler. Move some of the fins out of the way and then cut a small copper patch from a piece of copper tubing. Flatten the patch out and form it to the same radius as the copper line on the A/C unit. Sort of a band-aid, if you will. Braze all around it.
Can you fix a broken line on a copper compressor?
So much for copper. I didn't want to throw away a perfectly good compressor so with some spare parts lying around I went about repairing the broken line. This fix was unbelievably easy and if you have the same tools as I do, then for sure you can fix a broken line and even replace a busted compressor. As always safety first.
How do you seal a broken air conditioner line?
I used normal electronics grade solder to make an air tight seal between the line and valve. Step 2: Joining the Busted Lines. Using my tool set for air conditioning, I cut a length of spare tubing and expanded it. I basically used it as a splice and soldered the whole thing together. Step 3: Sealing a Cut Off Line.
How do I Stop my copper pipe from sweating?
Line the split up and make sure the adhesive glues the Rubatex split together. You want to create a vapor barrier to keep the humidity out and away from the pipe. That should fix your problem with the sweaty copper pipe.
Will the copper pipes in the air handler damage the floor?
I noticed the last time I went into the closet, the copper pipes that go into the air handler were sweating and dripping on the floor. It is a wooden floor, but I think if this continues, it will eventually ruin the floor and possibly the ceiling downstairs.
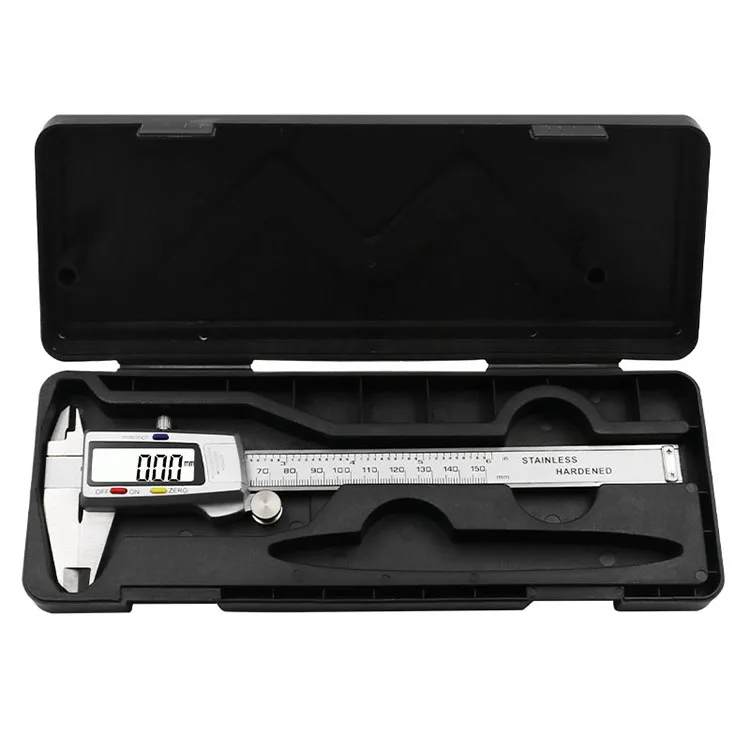
How do I fix a hole in my copper AC line?
0:244:08Highside Chemicals Instant HVAC/R Patch Permanent Fix for Copper ...YouTubeStart of suggested clipEnd of suggested clipNext apply bonding fluid a around. And over the crack hole or leak. Then immediately apply a coat ofMoreNext apply bonding fluid a around. And over the crack hole or leak. Then immediately apply a coat of bonding cells B on the bonding fluid a lastly apply more bonding fluid a onto the bonding cells B.
Can you solder copper AC lines?
Only flux the outside of the copper tubing that you're joining. Don't even use flux on the fitting (the edge). If you're using silver solder – that is, solder with 45 percent silver or higher – to connect copper to steel you must always use an acid-based flux.
How do you fix a broken copper line?
2:556:46Copper Pipe Repair -- Frozen Split or Puncture - YouTubeYouTubeStart of suggested clipEnd of suggested clipSlide it down here take the other cup and slide it up here put that new piece of pipe in there andMoreSlide it down here take the other cup and slide it up here put that new piece of pipe in there and slide this and this part over that make the solder joints. And we have our repair.
Can AC copper pipe be welded?
Uses: The connection between two copper pipes, one to two, quick connection, no welding, can be tightened with a wrench.
Is brazing better than soldering?
Soldering, in addition to having a lower processing temperature, typically results in a lower-strength joint than a brazed joint. For many applications, this is suitable and even desirable. The shear strength of brazed joints typically exceeds that of soldered joints by a factor of five.
How do you solder AC copper tubing?
1:5410:07How To Silver Solder (Braze) a Copper Pipe (A/C Line Repair)YouTubeStart of suggested clipEnd of suggested clipYou'll want to get a rod that contains phosphorus as their self fluxing. The need to apply any fluxMoreYou'll want to get a rod that contains phosphorus as their self fluxing. The need to apply any flux on the pipe scene silver solder melts at a much higher temperature.
How do you fix a leaking copper pipe without soldering?
0:001:03Connect Copper Pipe Without Solder - YouTubeYouTubeStart of suggested clipEnd of suggested clipLooking for an easy way to join solid copper together and you don't like to solder you don't knowMoreLooking for an easy way to join solid copper together and you don't like to solder you don't know how to these new push fit fittings are an excellent way to join copper.
How do you seal a leaking copper pipe?
Wrap & Seal Pipe Burst Tape is one of the most effective pipe repair tapes on the market. It stretches by 300% and is extremely easy to apply. You start by anchoring the Wrap & Seal next to the leak area before stretching the tape to its full length and wrapping it around the copper pipe until the leak is sealed.
Can you use JB Weld on copper pipe?
At least two different brands on the market -- JB Weld and Harvey's Epoxy Putty -- work equally well for the purposes of stopping leaks. Both adhere best to dry surfaces and are effective for blocking small leaks in copper and galvanized steel pipe.
Which welding is best for copper?
Welding processes such as Gas Metal Arc Welding ('GMAW') and Gas Tungsten Arc Welding ('GTAW') are commonly used for welding copper and its alloys, since high localized heat input is important when welding materials with high thermal conductivity.
Can you use compression fittings on air conditioner lines?
air conditioning compression fittings will make your job a breeze! Fix broken connections, repair damaged lines, block off failed rear lines, and create secure connections between different line sizes with help from S.U.R. &R.
Which is the best material to use on HVAC pipe brazing?
When brazing copper the best choice is always sil-phos. Only use silver braze on the brass and steel joints. This compound is very expensive so it is not commonly used when sil-phos can be used.
Why does my copper pipe sweat?
Moist, humid air will get inside the pipe insulation, even a pinhole leak, and cause the pipe to sweat. That can lead to water damage because the moisture it creates will accumulate. It may appear that the copper pipe is leaking water.
What happens if a pipe leaks long enough?
If the pipe has been leaking long enough, then it is possible that some of the moisture dripped down the pipe and went into the chase where the pipe runs. Sometimes, especially in new construction, the installer will use the void in the wall as his chase to run the pipes to the condenser.
What happens when you have a suction line?
The suction line typically operates below the dew point. When you have something that has a temperature less than the dew point temperature, then it will sweat. The moisture in the air is condensing, changing from a vapor to a liquid. An excellent example of this is a glass of ice water sitting on the table.
Can a cold water pipe cause sweating?
Any cold water pipe or cold pipe that is below the dew point will sweat. That includes the suction lines on your central air conditioning system, which should be a copper pipe. Water damage can be severe and needs mitigation; otherwise, you run into other problems that can affect your health and the structure itself.
Can you insulate a suction line?
Mold and mildew love dark, moist areas. It is vital that you only insulate the suction and not the liquid line. The suction line is the bigger of the two pipes that run to your condensing unit.
Do suction lines need to be insulated?
Even the part of the suction line pipe that runs in the chase should be insulated with Rubatex and have a good vapor barrier quality of insulation on it; otherwise, you get the problem described above in number one. Never insulate the smaller pipe. It should never sweat. If it does sweat, that will defy physics.
Step 1: Adding a Valve to the Vacuum and Fill Line
Newer refrigerators come with Schrader valves but this tiny unit just had its line crimped and brazed. I had an old brass valve so I went ahead and soldered this onto the line after cutting off the end. I used normal electronics grade solder to make an air tight seal between the line and valve.
Step 2: Joining the Busted Lines
Using my tool set for air conditioning, I cut a length of spare tubing and expanded it. I basically used it as a splice and soldered the whole thing together.
Step 3: Sealing a Cut Off Line
Using a small piece of tubing to make a crimp onto this line I filled it with solder and sealed off this unused line.
Step 4: Pulling a Vacuum
With my Manifold gauge set and vacuum pump hooked into the installed valve, pulled a vacuum for 20 minutes and locked off the manifold low pressure valve then turned off the vacuum pump. I let it sit like that for 15 minutes watching for any decrease in vacuum. Satisfied there are no leaks I went ahead to the next step.
Step 5: Adding R134a Refrigerant
I had a spare bottle left over from car work I did so I put a little into the vacuumed system. I estimate that about 1oz I needed for such a tiny system but I have no scale so I added tiny volumes and watch the low pressure gauge. Once I was satisfied enough was in the system I proceeded to power up.
Step 6: Testing!
It powered up successfully and the compressor hummed like a dream. I measured the power consumption and opened the can valve to let some more refrigerant in. Once the power consumption reached 69 watts I locked off the can valve. After 15mins and it used approximately 64watts. The low pressure gauge read -4.5 inHg.
Step 7: Practical Application Testing
The portable thermometer showed down to 4C with a power draw of 65watts.
