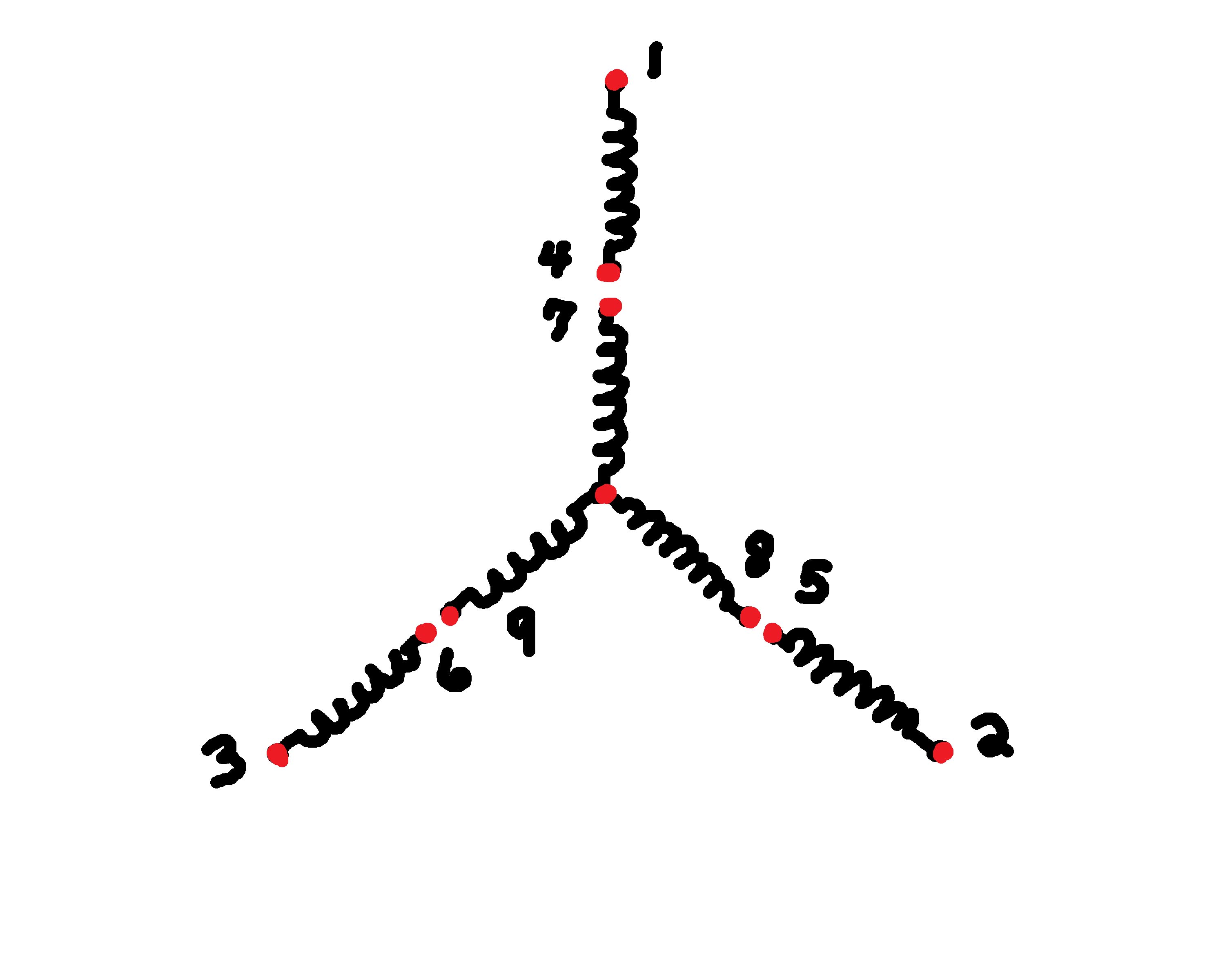
Cut the old windings free using a pair of wire cutters. Depending on the type of motor you’re working on and where the problem lies, the faulty windings may be found on either the stator
Stator
The stator is the stationary part of a rotary system, found in electric generators, electric motors, sirens, mud motors or biological rotors. Energy flows through a stator to or from the rotating component of the system. In an electric motor, the stator provides a rotating magnetic field that driv…
Full Answer
How do you fix an electric motor winding failure?
Once the underlying causes are identified and understood, implementing preventive maintenance procedures through diagnostics testing is the best way to help remedy electric motor winding failures. To diagnose a problem, there are three steps within each category to help quickly and efficiently manage the repair workflow:
How to insulate electric motor re-winding wire?
Usually if its that, the air does blow from the vents. Companies who are expert in or who provide electric motor re-winding services describe use of either varnish or a resin used to insulate the motor rewinding wire after repair.
How to varnish electric motor windings?
Dip and bake: electric motor windings are dipped in varnish and then baked in an oven 2. Trickle varnishing: the motor windings are heated and spun to distribute the varnish 3. Vacuum Pressure Impregnation (VPI) a vacuum pressure tank filled with varnish is used to fully impregnate motor windings and insulation with resin or varnish.
What is the process of rewinding a motor?
Given the sheer number of different motors and winding patterns, the rewinding process can vary greatly. However, it generally involves cutting the original windings out of the motor’s stator or armature and replacing them with new coils made from wire of the same basic type and gauge.

Can motor windings be repaired?
Motor Rewinding Procedures If an electric motor operates at too high a voltage, excess current flowing through the windings can cause them to become hot and burn out. While it is normally not practical to repair small, direct current (DC) motors that have burned out, other motors can be repaired by rewinding.
What causes motor winding failure?
Low Resistance The most common cause of motor failure, and arguably the most difficult to overcome, is low resistance. Low resistance is caused by the degradation of the insulation of the windings due to conditions such as overheating, corrosion, or physical damage.
How do you rewind an electric motor coil?
3:266:38Electric Motor Rewinding and Rebuilding Tutorial - YouTubeYouTubeStart of suggested clipEnd of suggested clipAfter the coils are in place wedging is added to prevent rotor to winding content and to furtherMoreAfter the coils are in place wedging is added to prevent rotor to winding content and to further insulate the.
What are the materials used for motor rewinding?
Here are some of the most desirable motor winding materials today:Motor Winding Material #1: Copper. Copper is the most common material used for motor winding construction. ... Motor Winding Material #2: Aluminum. ... Motor Winding Material #3: Silver. ... Motor Winding Material #4: Carbon Nanotubes.
How do you check motor winding failure?
Inspect the Motor Windings With a Multimeter To begin, set the multimeter to read ohms and then test the motor's wires and terminal. You should test the windings for a “short to ground” in the circuit and open or shorts in the windings.
How do you know if motor winding is good or bad?
Start by completely disconnecting the spindle motor from all power sources. Check each wire, including T1, T2, T3 and the ground wire. If the reading is infinite, your motor should be fine. If you get a zero reading or any continuity reading, you have either a motor problem or a cable problem.
How do you wind a coil by hand?
0:001:48How to Wind a Wire Coil with a Power Drill - YouTubeYouTubeStart of suggested clipEnd of suggested clipAnd do something like use duct tape to securely hold the tube onto the drill. Bit. Once you'veMoreAnd do something like use duct tape to securely hold the tube onto the drill. Bit. Once you've securely attached the tube to the drill bit secure the drill bit firmly in the drill. Chuck.
How many times can you rewind a motor?
So long as the shell exists, a motor can be repaired and reconditioned. The key is to remember that eventually that motor will need a burnout and rewind before it is insulated again. Then, with proper maintenance and smart reconditioning, there is no limit to how many times you can have that motor repaired.
How does a motor winding work?
Motor windings are conductive wires wrapped around a magnetic core; they provide a path for current to flow to create then magnetic field to spin the rotor. Like any other part of the motor, the winding can fail.
Which wire is used for motor winding?
Magnet wire is used in windings of electric motors, transformers, inductors, generators, headphones, loudspeaker coils, hard drive head positioners, electromagnets, and other devices.
What kind of wire is used in electric motor?
copper insulatedThe most common magnet wire is copper insulated wire used in electric motors – one of the greatest inventions of all time, right up there with the wheel and light bulb. Magnet wires can be divided into broad categories that include enameled wire, covered (or served) wire, or combinations of the two.
Which varnish is used for motor winding?
Jyoti-160-FD is a fast drying, synthetic resin based, class B insulting varnish (Temp. Index 130°C). The product provides good insulation and longer life to windings. Jyoti-160 finds application in insulation for medium and low voltage stator, wet grinders, winding of motors, fans, field coils, transformers and chokes.
What causes winding?
Winding occurs due to a temporary paralysis (spasm) of the diaphragm muscle. It is often caused by a direct blow to the abdomen and/or chest, a fall on the back, or a fall on the buttocks. Although it can be briefly traumatic, often leading the athlete to panic or hysteria, the condition is of no real significance.
What is the reason for motor winding resistance unbalance?
Resistance unbalance indicates connection issues that can be caused by loose connections, corrosion, or other buildups on the motor terminals. High Resistance connections can also occur which can cause excessive heat at the connection point that could lead to a fire damaging equipment and causing a safety hazard.
What are the main types of stator winding faults?
Different types of stator winding faults are (i) short circuit between two turns of same phase—called turn-to-turn fault, (ii) short circuit between two coils of same phase—called coil to coil fault, (iii) short circuit between turns of two phases—called phase to phase fault, (iv) short circuit between turns of all ...
How overheated motor winding can be diagnosed?
To verify overheating, you'll need to get the motor up and running again — this time with methods of monitoring it: Check the thermal reset button on your motor if it's equipped with one. This is the quickest, easiest way to qualify an overheat.
How to rewind a motor?
To rewind an electric motor, remove the motor's outer housing and use your hands to pull the armature out of the stator. Then, use a flat head screwdriver to pry open the tabs on the brush pads, and then cut through the wires and pull them out by hand. Once you have the coil off of the armature and stator, wind a new wir e of the same thickness and material into the armature. Be sure to coil the wire the same number of times to ensure a proper fit for conductivity, and secure the coil with tabs before reassembling the motor. For tips on identifying the coil pattern and handling the motor during disassembly and assembly, scroll down!
Where are the windings located on a motor?
The windings are long coils of copper wire typically located around the stator. They channel electromagnetic energy into the rotor to cause the motor to turn.
How to force armature out of stator?
Force the armature out of the stator by hand. Once you’ve removed the upper endplate from the motor housing, guide the armature straight out the bottom of the circular stator, along with the attached lower endplate. You'll encounter some resistance from the magnets around the stator, which means you may have to push a little harder than you might expect before it will give way.
What is the armature of a motor?
The armature (also known as the “rotor”) is a small bearing-like piece in the center of the motor construction. When it receives the magnetic force of the stator and windings, it spins, powering the motor. The windings are long coils of copper wire typically located around the stator.
Why do you wear gloves on stators?
Wear gloves to protect your hands and avoid transferring the oils from your skin to any part of the stator or armature .
How to remove motor housing?
On most types of small motors, this will require you to unfasten four screws from around a small endplate on the top and bottom of the unit. Once they’re out of the way, you’ll be able to see each of the motor’s primary internal components, including the stator, armature, and windings.
Can you cut out a winding?
Cutting out the spent windings can be painstaking work. It may be necessary to sever one wire at a time to make removing the coils more manageable.
How many windings are in a single phase motor?
Reader comments on single phase & 3 Phase motors. Most single phase motors have two sets of windings. The main or primary windings are directly connected to the power lines while the motor in running. The second windings are usually thinner wires physically offset from the main windings inside the motor.
Which way do electric motors run?
In short: check the motor label: uni-directional electric motors run just one way: clockwise (CW) or counterclockwise (CCW) but not both. Bi-directional & self-reversing electric motors run in either direction, CW or CCW. Some electric motors can start and run "backwards" following damage to the motor's start capacitor or windings.
What is a stator in a motor?
Electric motor stator: the stator consists is a device or core containing start and run windings (of copper wire) wound around a central core to create a magnetic field. Electric motor windings: the two windings are used to create an electrical field in the stator.
What is start winding?
Definition of Start winding: in an A/C (alternating current) electric motor electrical current flowing through the start winding is used just to get the motor spinning from a stopped condition. The start winding is disconnected, usually by a centrifugal switch, when the motor is up to speed.
Why is a start switch necessary?
This feature is necessary because depending on the position in which the rotor stopped when the motor last turned off, the rotating electrical field created by the run winding can't start the motor.
How to diagnose a failed start winding?
A trained service technician may sometimes diagnose a failed start winding or failed start switch (centrifugal switch) by spinning the motor manually (potentially dangerous!). If the motor keeps running we suspect a bad start winding or bad start switch (see diagnostic table details
How to get more life out of a motor?
simply swap in a new start capacitor. That may give you some more life out of the motor.
What Causes Electric Motor Winding Failures?
What causes electric motors to fail? Unfavorable operating conditions—whether electrical, mechanical, or environmental—can dramatically shorten the life of an electric motor. The Electro-Mechanical Authority (EASA) cites many causes of electric motor winding failures including:
What causes a winding to fail?
This includes single-phased winding failures (wye- or delta-connected) caused by an opening from a blown fuse, open contactor, broken power line or bad connection.
Why is the insulation in a stator deteriorating?
There could also be thermal deterioration in all phases of the stator winding typically due to load demands exceeding the rating of the motor or by very high currents in the stator winding due to a locked rotor. It may also occur as a result of excessive starts or reversals.
What is the best way to monitor an electric motor?
As part a regular maintenance program, next-generation diagnostic and maintenance tools that include connected tools, sensors and software offer the best way to monitor an electric motor’s health.
How to get a complete picture of a maintenance system?
To get a complete picture, evaluate the likely failure modes and match the right maintenance technologies with the most likely failure mode. Maintenance software and data gathering devices that integrate with third-party solution providers are ideal to accomplish this.
What are the most common mechanical faults?
The most common mechanical faults are shaft imbalance, looseness, misalignment, and bearings. Often these mechanical faults are related: shaft imbalance, looseness, or misalignment left uncorrected will cause increased forces on the bearings which leads to rapid wear of the bearings.
Why are electric motors important?
However, electric motors can be prone to any number of issues that lead to motor faults and failures, which can disrupt business operations, decrease productivity and adversely impact a company’s bottom line.
Why is my motor winding open?
A common cause of an open winding is undersized lead lugs. Charred connections in the motor’s connection (terminal) box are a sure indication of this problem. Open windings are also caused by shorted turns, phase-to-phase shorts, ground-to-frame shorts, faulty internal coil-to-coil connections, severe overloads, and physically damaged coils.
What causes a motor to be grounded?
The problem is usually found in a slot, where the slot insulation has broken down. Water is the most common cause of a grounded winding . A solid ground requires rewinding or replacing the motor.
Why do you skim a rotor on a lathe?
If the rotor drags on the stator and the bearings aren’t worn , it’s common practice to “skim” the rotor on a lathe. The process increases the air gap, which increases the no-load amperes. The increased amperes are similar to a misaligned rotor and stator iron. The magnetic circuit is degraded, so it takes more amperes to magnetize the motor’s iron.
What causes a short in a motor?
Shorted turns are caused by nicked coil wire, high-voltage spikes, conductive contaminants, overheated winding, aged insulation, and loose, vibrating coil wires.
Why do coils short?
A short forms when one or more turns of a coil are bypassed because of an insulation breakdown between wires. The resistance that the shorted turns develop is eliminated from its phase winding, resulting in increased amperes. When there are a few shorted turns in one of the three phases, a closed-loop circuit is formed by the turns within the short. As the motor runs, lines of force (from AC current flow) cut the wires in the closed-loop circuit.
What is the most important factor in AC motor resistance?
The most of the resistance to current flow in an AC motor is furnished by inductive reactance. The resistance of the wire in a complete phase is a very small percentage of the motor’s total impedance (resistance plus inductive reactance). Inductive reactance makes each turn very significant in the motor’s ampere demand. Each turn supplies much more inductive reactance than resistance.
What happens if a motor is open circuit?
Its power will drop to about half, and the motor won’t start. If the motor’s internal connection is multicircuit, it will start but will have reduced power. An open circuit will cause the magnetic circuit to be unbalanced. Under normal load the motor will run more slowly and will overheat.