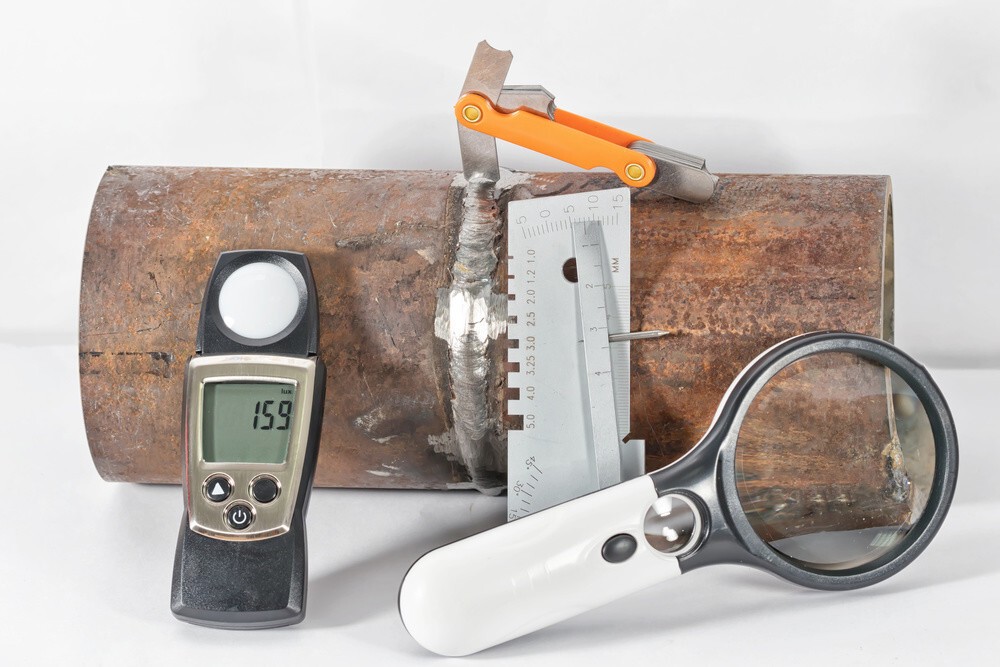
- Control the length of your arc
- Control the temperature appropriately (don’t make it too low)
- Keep your movements smooth and even
- Be patient and allow your groove time to properly fill in
- Focus on the toes of the weld as that is the most likely area for an undercut
- Remember that it’s primarily about the process
- Pay attention during your weld process
What is undercutting in welding?
Undercutting is a groove that develops during a weld. It can show up in the base metal near the toe or root of your weld. Undercut is a side effect of the weld metal not filling the grooved area. Your weld is bound to have cracks along the toe of the weld.
How can I prevent undercut grooves in welding?
If not, the weld might be susceptible to undercut grooves. To prevent this, try to reduce the weaving size or produce the weld in a multi-pass technique. In the case of a metal active gas, improper selection of gas shielding is also one cause of undercutting. Using carbon dioxide with inert gases may provide good results in welding carbon steels.
Can an undercut be repaired?
In the welding industry, whether or not to repair an undercut can be a difficult one. Costs should be weighed against benefits before arriving at a decision. No matter which option is chosen, repairing an undercut is possible and can be easy, depending on the severity.
What is a crown undercut in welding?
A crown undercut or external undercut occurs near the weld area’s toe or crown on the parent metal. In a radiograph, the crown undercut can show up as a dark line around the welded area’s edge. The reason for an undercut is quite straightforward, so it’s time to start learning what causes one.
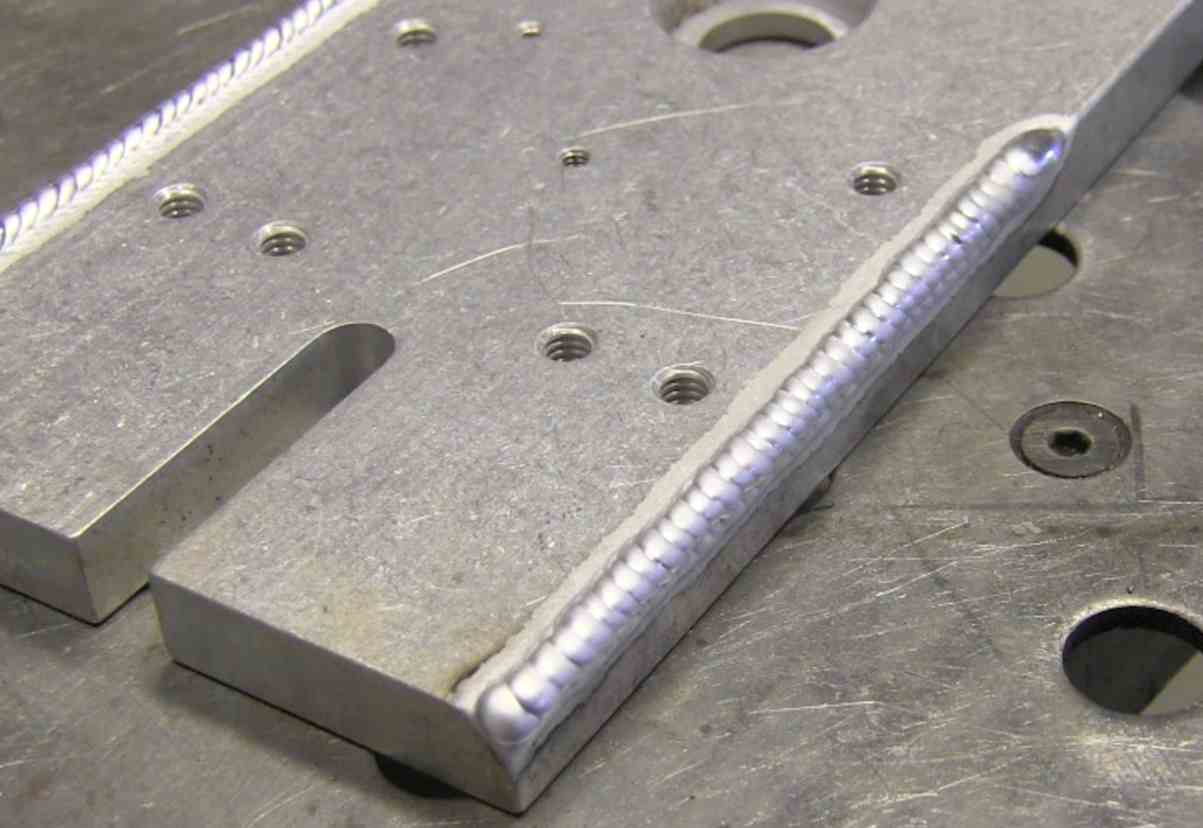
What is undercut How is it prevented?
One of the most important reasons for the undercutting during welding is the use of high heat during an operation near the free edges. This causes the melting of the main metal or the previous weld metal. To avoid this, reduce the welding current, which may require a reduction in arc speed.
How do you fix an undercut on a pipe?
0:0710:09How to Fix Undercut on Pipe Root and Cap - YouTubeYouTubeStart of suggested clipEnd of suggested clipI'm going to show you the undercut we have the reasons you get undercut is misaligned pipe second isMoreI'm going to show you the undercut we have the reasons you get undercut is misaligned pipe second is running too high of a amperage. And third actually is not adding enough filler wire.
What step will eliminate the undercut defect in arc welding?
Remedies/Prevention of Welding undercut Use the right electrode size with correct positioning; between 30 to 45 degrees angle. Reduce the length of the arc and lower the voltage. Weld in flat positions. Use proper current with attention to thinner areas and edges.
Why do I keep getting undercut in my welds?
Undercut can occur for several reasons: Excessive heat from high current and voltage settings. If the travel speed is too fast, the electrode moves away from the weld pool prematurely. If edges are not prepared properly dirt or grit on the welding surfaces tends to block heat transfer which can cause undercutting.
How do you get rid of an undercut?
How to Prevent Undercut in Stick Welding: 12 Golden TipsControl Your Arc Length.Control Weld Angle.Reduce Current.Slow Down the Travel Speed.Reduce the Weave Width.Choose the Correct Welding Position.Consider Which Electrode You Are Using.Allow the Base Metal to Cool.More items...
What is remedy for undercut?
Remedies of Undercut Decreasing the travel speed of the electrode, but should not be too slow. Using poor welding methods. Applying the multipass technique. Use of incorrect gas shielding and filler metal.
How do I stop my undercut from MIG welding?
With MIG, too high of a voltage setting will dig into your base material – despite filler wire being added, high heat can still cause undercut. We recommend incrementally lowering your voltage until your undercut disappears. Start with a small reduction, and then go from there.
How do you fix a welding defect?
0:358:18How to Fix Common Weld Defects | Part 4 of 4 - YouTubeYouTubeStart of suggested clipEnd of suggested clipThe the vertical and horizontal coupe. On here so I want to make sure I get equal leg length orMoreThe the vertical and horizontal coupe. On here so I want to make sure I get equal leg length or equal weld on the vertical and the horizontal piece or the flat piece.
How does undercut affect a weld?
An undercut is a surface and subsurface defect resulting from grooves within the parent metal area. Like all other defects, instead of improving the joint strength, it introduces weak points that often propagate structural failure.
What does welding undercut look like?
1:078:39WELDING DEFECTS!! Porosity, Arc Strikes, Undercut - YouTubeYouTubeStart of suggested clipEnd of suggested clipSo undercuts pretty common what that is it's an eroded edge along the toe of one if not both of theMoreSo undercuts pretty common what that is it's an eroded edge along the toe of one if not both of the toes of the weld.
How much undercut is allowed?
undercut shall not exceed 1/32 in., with the following exception: undercut shall not exceed 1/16 in. for any accumulated length up to 2 in. in any 12 in. ..." Depth of undercut that is not more than 1/32 in. is acceptable, period!
How do you fix an uneven undercut?
4:485:53How to Fix an Uneven Undercut Haircut - TheSalonGuy - YouTubeYouTubeStart of suggested clipEnd of suggested clipYou can try to do it. Yourself at home with cutting with scissors you know using a comb and justMoreYou can try to do it. Yourself at home with cutting with scissors you know using a comb and just trying to find where the balance is.
How do you blend a disconnected undercut?
7:1219:33How to Blend a Disconnected Undercut - MUST WATCH - YouTubeYouTubeStart of suggested clipEnd of suggested clipThis way because there's a disconnected part there and now we're combing over it and the best andMoreThis way because there's a disconnected part there and now we're combing over it and the best and most simple way to take this on is when you lift up the hair with your comb.
How do you blend a grown out undercut?
3:056:23How to Grow out an Undercut - TheSalonGuy - YouTubeYouTubeStart of suggested clipEnd of suggested clipSo you may have to cut the top quite a bit in order to create some sort of illusion. Of it beingMoreSo you may have to cut the top quite a bit in order to create some sort of illusion. Of it being balanced all right and also. The long term goal with your hair.
What's the difference between an undercut and a disconnected undercut?
0:226:19Disconnected Undercut: What to Tell Your Barber - YouTubeYouTubeStart of suggested clipEnd of suggested clipAnd undercut the haircut is disconnected. Because the length on my sides compared. To the length onMoreAnd undercut the haircut is disconnected. Because the length on my sides compared. To the length on my top are two completely different sizes. There's no fate let me show you.
How to Avoid Undercut in Welding?
There are so many ways to avoid weld undercuts. Some of these include:
How to Fix Undercutting?
The way to fix an undercut weld, you don’t have to grind the uneven surface or the undercut and then start over again. Grinding won’t fix the problem. An undercut part has a lack of filling material. So, even if you grind the surface, you’ll still have to mold or patch the hole to fix the problem.
What Causes Undercut?
Undercutting can also occur when welding conditions generate too much heat input, causing excessive melting of the base metal.
What are undercuts in welding?
Undercuts in welding are among the most common welding defects every welder encounters at some point in their careers. Although the welded area becomes weak and prone to cracking, undercuts can be greatly minimized with proper welding techniques.
What is the first step in preventing welding defects?
Knowing what causes undercuts, as with any welding defect, is the first and most important step in preventing this defect. Just finding out how they occur can eliminate any welding defect.
Why are undercuts dangerous?
They appear more frequently in fillet and butt joints. Undercuts are mainly considered dangerous due to their tendency to reduce the thickness of parent metal. As a result of this reduction in thickness, quality, and strength of the weld and structure are reduced.
Why does weaving cause undercuts?
Insufficient weaving skills can increase the welding speed; therefore, causing undercuts. For example, weaving too fast causes uneven distribution of heat, resulting in inconsistent melting of metal, leading to undercuts.
Why does welding fail?
While welding, some welding processes can fail due to low travel speed. Low travel speed can lead to undercuts, burn through, incomplete penetration, interspatter, cracking, and other defects. Travel speeds must be such that the weld metal can fully fill the joint area.
What is excessive arc length?
Excessive Arc Length. Welding arcs are the zones between the tip of the welding rod and the material to be welded. When the arc is larger than the electrode diameter, the metal covers a greater area than intended, which leads to decreased undercuts.
Why do welders use large electrodes?
Using large electrodes can lead to undercuts, as electrolysis removes too much metal. Welding rods of the correct size should also carry high currents without interfering with the supply of molten metal or deforming the metal. Extremely small electrodes will not generate enough molten metal, resulting in welding defects.
Why does my welding undercut?
There are several possible causes of an undercut, ranging from poorly done welding to incompatible weld-parent material. We’ll cover all the ins and outs below.
What is undercut in metal?
An undercut is a surface and subsurface defect resulting from grooves within the parent metal area. Like all other defects, instead of improving the joint strength, it introduces weak points that often propagate structural failure.
What is the arc of a welding weld?
Arc is the gap between the tip of the electrode and the surface of the weld . Remember, there are four basic welding positions: horizontal, vertical, flat, and overhead. These positions affect arc length variation. A wide arc length results in more molten metal being deposited than was actually needed, which leads to an undercut. Nonetheless, arc length variation is required in most complex welding projects. So, ensure the length is in line with the requirements of your project. The standard arc length is approximately equal to the size of the core wire of the electrode.
Why does a welder have uneven heat distribution?
However, there are instances where the welder can experience uneven heat distribution due to poor weaving. As mentioned earlier, you will end up with uneven curing. To avoid this inconsistency, ensure you hold the electrode properly while welding. Also, when an undercut occurs, the parent material experiences improper melting because there is no proper fusion between the weld material and base material.
Why do welders use multipass?
Multi-pass involves piling weld material on top of the other until the duct is filled. Before taking another pass, you should allow the deposited material to cool off and allow for curing to take place. The multi-pass method assists in stabilizing metal fusion, creating excellent structural resilience.
What happens if you have a large electrode?
Electrodes come in different sizes and designs. If you opt for a large one, the amount of molten metal deposited also increases, forming an undercut. Likewise, if the electrode is too small, the amount of molten metal being deposited becomes insufficient, leading to surface defects.
What is the best angle to hold a welding joint?
The best holding position would depend on many factors, such as the type of material and nature of the welding joint, among others. Generally, the holding angle should range from 30-45 degrees for general welding.
What Causes Undercut In Welding?
Undercut in welding, as what we’ve said is a groove formation at the weld toe, reducing the cross-sectional thickness of the base metal. This often results in weak weld and workpiece. Some of its causes include the following:
Where does undercutting occur?
Types Of Undercutting. Also known as the root undercut, it happens in a butt joint weld alongside the base metal next to the weld’s root. In pipe welding, it’s seen inside the pipe on the narrow edge. One more form of the internal undercutting can be seen within the weld itself.
Why do welders weld in flat positions?
To prevent this, you can weld in a flat position to make sure that there is enough electrode consumption. Proper Welding Technique. The issue of undercut may also arise when a welder tries making a weld run using an excessive style of weaving.
What is an unacceptable weld profile?
Known as unacceptable weld profiles or defects , these imperfections negatively affect the durability and strength of a weld. One of the more common weld defects in welding is undercut. Undercut or undercutting is a weld defect that results in the reduction of the thickness of a material that’s being welded.
Why is angle important in welding?
Welding angles play an important role in the production of defect-free beads. For this, you should use correct angles to direct more heat into thicker components. Right Heat Input. The heat or amperage settings are one of the major causes of undercut in welds .
Why are there defects in welding?
Defects are so common in any kind of manufacturing, including welding. In the process, there might be deviations in the size and shape of the metal structure. It may also be due to the use of improper welding processes or wrong welding techniques. Known as unacceptable weld profiles or defects , these imperfections negatively affect ...
Why is the bottom plate of a T-joint welded?
Since the bottom plate is welded in the middle, it actually makes sense in focusing more heat on it as it can absorb more. A lot of beginners forget about this basic rule on how metal responds to heat.
How to minimize welding undercuts?
One of the best methods to adopt in order to minimize the level of undercuts in welding is to employ the multi-run technique. This technique supports all of the above-mentioned preventions and can also help achieve satisfactory results with improved mechanical properties.
Why does welding undercut?
The major cause of undercuts in welding is when the operator (welder) uses a high welding current or welds with fast travel speed. At the same time, the use of incorrect shielding gas, incorrect welding angle, wrong weld ing technique, and position are some of the primary causes of this welding flaw.
Why is welding angle important?
It’s generally known that welding angles play a crucial role in producing flaws-free welds. If the welder uses an incorrect angle which transfers more heat to the free edges more than the required, the weld is likely to be prone to undercut. Therefore, one is advised to use the correct angles in order to transfer the appropriate heat to the free edges.
Why does a weld bead look peaked?
High travel speed. When the travel speed is very high, the weld bead will appear very peaked. This is because of its extreme fast degree solidification.
What is undercutting welding?
Undercutting is a crater or groove that occurs near the toe of the weld. Undercutting in welding occurs when the weld metal failed to fill-in the grooved area. The result of which is a weak weld that is prone to cracking along the toes. In that case, the edge of the weld assumes a U-shape. Undercutting in welding may occur as a result ...
Why does my weld have a U shape?
Undercutting in welding may occur as a result of high travel speed, poor welding techniques, excessive heat, and too high amperage.
Why does welding with high travel speed cause undercutting?
What happens while welding with high travel speed is that some portion of the parent material is drawn into the molten metal and never came back because of its extremely fast solidification rate, leaving a depression along the edges.
Different Types of undercut
There are many different types of undercuts. The most common types of undercuts are Internal and external.
What Causes undercut in welding?
Whether you’re a beginner or an experienced welder, undercut welds are inevitable. Many mistakes can result in an undercut. Below is a list of a few causes of an undercut weld:
9. Welding too Fast
Welding too fast can cause an undercut in welding. When you are trying to fill a large gap between two pieces of metal, the arc will melt both sides which cool down into two separate pools before the rod melts into it. This results in an inadequate weld that is weak and has no penetration.
Tips to Prevent Undercut in Welding
Undercuts are usually caused by some inaccuracy caused during the welding process. However, undercuts can be prevented or minimized by doing some precautions such as:
How to Fix or repair Undercut in Welding?
To fix an undercut in welding, you simply have to find where the undercut was made. It might be easy or difficult depending on the circumstances of your weld.
What is undercut in electrical engineering?
Undercut is a discontinuity / defect that can be eradicated easily by three basic criteria - correct wire / electrode size, correct interpass temperatures and correct technique.
What is undercut in a notch?
Undercut is a LOSS of material, so grinding isn't helping other than blending the notch out of the material. If you want to grind the notch, then place a quick pass back over where the missing material is.
Where is the weld starting?
The weld is started at the top of the shear tab and stops one weld size from the bottom, where welders tend to hold back a little on the weld progression to allow the weld to build up so as to eliminate the crater. The problem has been they hold back long enough to create undercut.
How to avoid notches in base metal?
An accepted practice to avoid notches in base metal is to stop fillet welds short of the edge of the base metal by a length approximately equal to the size of the weld. In most welds, the effect of stopping short can be neglected in strength calculations.
