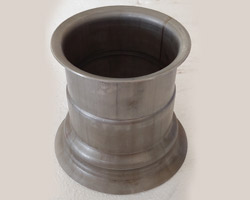
Basic body work part 1: Repairing rusty sheet metal
- Step 1: Clean Up Your Workplace. Now that you’re ready to get to work, you need to clean off all of the old paint,...
- Step 2: Sparks Fly. After we removed most of that nonmetallic filler with our wire brush, we mounted a grinding wheel on...
- Step 3: Make the Cut. We have found that initially cutting the patch panel from...
How to install sheet metal?
Solidworks sheet metal tutorial
- First Create a New Part.
- Right-click on the toolbar and activate Sheet Metal.
- Click on the top plane and then create a new sketch.
- Now, sketch and use Smart Dimension to give a dimension to the design.
- Click on the Sheet Metal tab, select Base Flange/Tab and give 1 mm to the sheet metal parameters.
How to debur sheet metal?
Your problem, our solution
- Burrs do not look professional and qualitative, from an aesthetic point of view it is recommended to deburr.
- Chance of minor injuries to assembly personnel, due to sharp burrs.
- Burrs can cause problems during assembly due to incorrect fitting.
- Burrs pose a risk to the proper functioning of the installation in which they are installed. ...
How expensive is sheet metal?
The Sheet Metal Market is expected to have a CAGR of 3.76% during 2020-2024. What are the pricing models followed by buyers? Volume-based pricing, spot pricing, and cost-plus pricing model are ...
How to repair rusted metal without welding?
Step-By-Step Guide on How to Use Two-Part Epoxies
- Use a Flapper Wheel. Affix a flapper wheel with 60 grits onto a 4.5-inch long angle grinder, and then, don your security glasses.
- Clean It Using a Rag. Clean the sanded metal surface using a rag. ...
- Thoroughly Amalgamate Two-Part Epoxy Putty in Equal Parts. ...
- Apply It on the Rusted Hole. ...
- Let It Cure. ...
- Detach the Flapper Wheel. ...
- Sand It. ...

How do you repair torn sheet metal?
All you have to do is cut a clean, square hole large enough to accept a raised lip on the patch, carefully weld the patch to the underside of the hood, fill the gap between the hood and the patch with body putty, and sand it smooth. Unfortunately, there may still be times you need to create your own sheet metal patch.
How do you fix sheet metal without welding?
Epoxy and tape are two common no-weld hole repair options. These do-it-yourself approaches are effective when repairing a small hole rather than a significant tear. Specialty epoxy and tape products are designed to patch steel and metal.
What gauge sheet metal should I use for auto body repair?
Automotive sheet metal once ran in the range of 18-gauge, which was 48 thousandths of an inch thick (actually 0.0478 inch). 20-gauge became common in more recent times, and this meant 0.0359-inch-thick metal—still a lot to work with in-bumping and metal finishing.
How do you fix cracked metal?
0:001:00JB Weld for Metal Repair - YouTubeYouTubeStart of suggested clipEnd of suggested clipUse high heat epoxy putty stick. Most jb weld metal repair products set quickly and when completelyMoreUse high heat epoxy putty stick. Most jb weld metal repair products set quickly and when completely cured can be sanded drilled.
How do you fill a hole in sheet metal?
You can use a hard piece of cardboard, a kit applicator, or a putty knife. Make sure that you apply epoxy until the entire hole is filled or repaired. Epoxy will form over the metal surface and the edges of the hole will overlap a bit. Allow the epoxy to harden.
How do you bond metal to metal without welding?
Bonding compound: Loctite Weld Another option for gluing metal is Loctite Epoxy Weld Bonding Compound. A convenient alternative to welding, it's the strongest solution for bonding most metals, including iron, steel, aluminum, brass, copper, and pewter.
What thickness is car body panels?
Even though you might only need a couple of square feet of sheet metal to repair your car, you will have to buy a standard 8 foot by 4 foot sheet from your local steel stockholder.
How do you weld auto body sheet metal?
0:034:08Lap Welding Auto Body Sheet Metal - Made Easy - YouTubeYouTubeStart of suggested clipEnd of suggested clipRight where I want it so put it there 45 degree angle bang. Put it there 45 degree angle zap zap zapMoreRight where I want it so put it there 45 degree angle bang. Put it there 45 degree angle zap zap zap zap zap zap zap zap zap all the way along another thing is you can roll.
What type of sheet metal is used in cars?
Sheetmetal generally comes in three forms—mild steel, aluminum, and stainless steel. Of these, aluminum and mild steel are by far the most commonly used for automotive projects. Sheetmetal fabricators prefer aluminum for dashboards, bulkheads, and most other purposes because it is light, soft, and easy to work with.
How do you fix cracked metal without welding?
Another effective way the cracks can be fixed without welding is brazing. Unlike the traditional welding technique used to repair metal items, brazing uses minimal heat to fix your cast iron pieces. This technique is commonly used to correct cracks on cast iron items.
Is there a filler for metal?
Permatex Liquid Metal Filler is an easy-to-use filler that can be drilled, filed, sanded and painted. It forms a long-lasting, metal-tough bond and works on metal, wood, and concrete.
What is the best epoxy for metal?
1. Devcon Plastic Steel Epoxy. The strongest epoxies will often have a longer setting time. Devcon's Plastic Steel Epoxy is one of the best choices for all types of metals; it contains a steel alloy for an impressive final tensile strength of 2,600 PSI.
What can I do instead of welding?
Alternatives To WeldingBrazing. Brazing is similar to welding but instead of melting two pieces of metal to join them together, you melt a filler metal that you place between the two metals that you want to join together. ... Soldering. ... Riveting. ... Metal stitching. ... Looking for sheet metal machinery?
How do you join two pieces of metal together?
1:153:06Different Ways To Join Metals Without Mechanical Fasteners - YouTubeYouTubeStart of suggested clipEnd of suggested clipAnd brazing is when you're brazing you're actually smelting one metal on top of another kind of likeMoreAnd brazing is when you're brazing you're actually smelting one metal on top of another kind of like applying glue.
How do you bond metal to metal?
Loctite Epoxy Weld Bonding Compound is a great choice. This two-part epoxy excels at bonding metal to metal as a convenient alternative to welding. Use it to repair machinery, appliances, pipes, auto components, etc. It can be drilled and machined once it's cured and can stand up to high temperatures.
How do you fix a big rust hole without welding?
0:1417:27DIY Repair Rust Holes with Basic Tools and NO Welding! - YouTubeYouTubeStart of suggested clipEnd of suggested clipRight here at home and we're going to show you today how to fix little rust holes without doing anyMoreRight here at home and we're going to show you today how to fix little rust holes without doing any welding. And just using some reinforced body filler.
How to repair a crack in a sheet metal airplane?
The common fix is to "stop drill" the crack with a small diameter drill bit. In other words, you drill a small hole at each end of the crack in the hope of stopping its growth. This fix is not a repair. To repair the crack, after you stop drill it, rivet a small sheet metal patch of the same type and thickness metal over the crack to restore the area's strength and to keep vibra tion from acting on it further (see Figure 1).
How to remove rivets from sheet metal?
When removing rivets, do not drill any farther than the rivet head. Do not attempt to drill into the sheet metal itself. After drilling into the head, use a pin punch to pry off the rivet head. Then use a punch smaller than the rivet shank to drive the rivet out of the hole. Your goal is to remove the rivet without enlarging its hole or damaging the sheet metal.
Why are rivets missing?
Finding missing rivets is not uncommon. Their loss could be the result of improper installation, corrosion, or some sort of underlying damage. You need to find out why it's missing and investigate the surrounding area for additional damage. Look for damaged rivets, the heads of which may be slightly slanted or raised. If you can place a 0.020-inch feeler gage under the rivet head, it's been stretched-an indication of damage.
How to determine strength of rivet?
The strength of a riveted piece is based upon the rivet's expanded diameter. This is why it's important to drill out the rivet using the proper size drill and to replace it with a rivet of the proper diameter and length. The length must be such that the shop head (driven head of the rivet) must expand to form a head that is 1.5 times the diameter of the shank. Rivets may be cut to proper length using a rivet cutter.
What is the first step in a repair process?
The first step in any repair process is assessing the damage to determine whether it's simple or major. Minor damage to a sheet metal structure includes missing or damaged rivets, scratches or small dents, a small crack, and a corroded sheet metal surface. Damage that exceeds the scope of these items is, in most cases, major. For example, deformed rivets often indicate damage to a sheet metal structure, and your inspection should include an area well past the deformed rivets.
How to repair a small dent in a car?
Bondo filler tends to shrink after being applied. Apply the SuperFil with a squeegee, let it dry overnight , sand it smooth , and touch up the area with paint.
What is a damaged control surface?
A damaged control surface is an example. The repair might be simple, but any change to the surface affects its balance, which can lead to flutter in flight. To complete the repair, you'll need to rebalance the surface and perhaps other components or surfaces attached to it.
What volts do you use for sheet metal repairs?
Time for tool selection. Depending on where we’re working, we’ll use either a Daytona MIG 140-amp, 110-volt MIG welder or an HTP 160-amp , 220-volt MIG welder for our sheet metal repairs. We used the Daytona MIG machine this time.
What to use to cover up bare metal?
All of that bare sheet metal should be covered up so that it doesn’t start to rust. Typically, we first apply a phosphoric acid metal treatment like Ospho to the area. We follow that with an etching primer.
How to secure a patch in place?
While wearing protective gloves, hold the patch where you want it and use one good tack weld to secure it in place. Check that the patch is in the correct spot and give it another tack weld. Apply a few more tack welds around the perimeter of the patch, bending the sheet metal to shape if necessary.
Can you cut a patch panel from sheet metal?
We have found that initially cutting the patch panel from your sheet metal can be a little tricky. Cutting a template out of cardboard is a great first step. Some trial fitting and trimming will make it pretty obvious when the cardboard patch is the correct size and shape; then you can trace the shape of the cardboard onto the sheet metal and cut out the patch panel.
Can you patch a car panel?
If the panel is welded to the car itself or if replacing the entire panel is not an option, then the question becomes whether to use a patch panel that is specific to that application or to fabricate one from generic sheet metal stock. If a repair patch is available, get it. It’s often a lot less time consuming to go with a preformed replacement panel than to cut, bend and form a new one.
Can you weld around the perimeter?
Now that the patch is on there, you can start stitch welding around the perimeter. To limit the amount of heat that one area sees, jump around a bit and avoid laying one continuous bead. This method lessens the chance of warping and the amount of body filler you’ll need later.
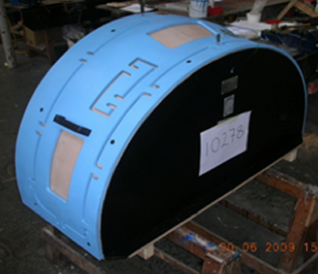